Atomically Precise Assembly of 2D Materials Paves Way for Next-Generation Electronics
Key Highlights
- Atomically clean interfaces: The new stamp design has enabled the creation of atomically clean interfaces between stacked 2D materials over extended areas, a significant improvement over existing techniques.
- Reduced strain inhomogeneity: The rigidity provided by the new stamp design has been shown to greatly reduce strain inhomogeneity in assembled stacks.
- Scalability: The team has demonstrated clean transfer of mm-scale areas of 2D materials, paving the way for the use of these materials in next-generation electronic devices.
This ubiquitous transfer-induced contamination, along with the variable strain introduced during the transfer process, has been the primary obstacle hindering the development of industrially viable electronic components based on 2D materials.
Researchers at the University of Ò°ÀÇÉçÇø have made a breakthrough in the transfer of 2D crystals, paving the way for their commercialisation in next-generation electronics. This ground-breaking technique, detailed in a recent publication, utilises a fully inorganic stamp to create the cleanest and most uniform 2D material stacks to date.
The team, led by from the , employed the inorganic stamp to precisely 'pick and place' 2D crystals into van der Waals heterostructures of up to 8 individual layers within an ultra-high vacuum environment. This advancement resulted in atomically clean interfaces over extended areas, a significant leap forward compared to existing techniques and a crucial step towards the commercialisation of 2D material-based electronic devices.
Moreover, the rigidity of the new stamp design effectively minimised strain inhomogeneity in assembled stacks. The team observed a remarkable decrease in local variation – over an order of magnitude – at 'twisted' interfaces, when compared to current state-of-the-art assemblies.
The precise stacking of individual 2D materials in defined sequences holds the potential to engineer designer crystals at the atomic level, with novel hybrid properties. While numerous techniques have been developed to transfer individual layers, almost all rely on organic polymer membranes or stamps for mechanical support during the transition from their original substrates to the target ones. Unfortunately, this reliance on organic materials inevitably introduces 2D material surface contamination, even in meticulously controlled cleanroom environments.
In many cases, surface contaminants trapped between 2D material layers will spontaneously segregate into isolated bubbles separated by atomically clean areas. "This segregation has allowed us to explore the unique properties of atomically perfect stacks," explained Professor Gorbachev. "However, the clean areas between contaminant bubbles are generally confined to tens of micrometres for simple stacks, with even smaller areas for more complex structures involving additional layers and interfaces."
He further elaborated, "This ubiquitous transfer-induced contamination, along with the variable strain introduced during the transfer process, has been the primary obstacle hindering the development of industrially viable electronic components based on 2D materials."
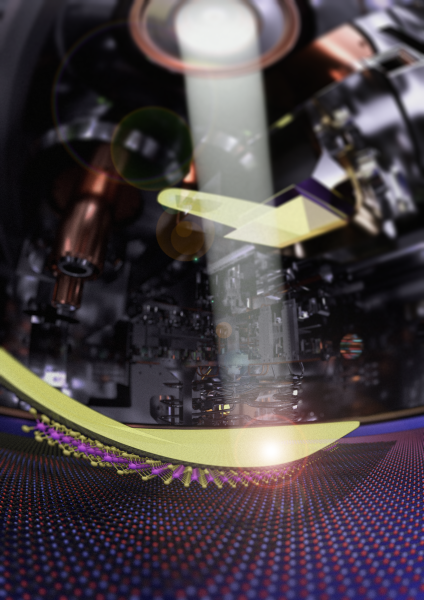
The polymeric support used in conventional techniques acts as both a source of nanoscale contamination and an impediment to efforts to eliminate pre-existing and ambient contaminants. For instance, adsorbed contamination becomes more mobile at high temperatures and may be entirely desorbed, but polymers cannot typically withstand temperatures above a few hundred degrees. Additionally, polymers are incompatible with many liquid cleaning agents and tend to outgas under vacuum conditions.
"To overcome these limitations, we devised an alternative hybrid stamp, comprising a flexible silicon nitride membrane for mechanical support and an ultrathin metal layer as a sticky 'glue' for picking up the 2D crystals," explained, second author of the study. "Using the metal layer, we can carefully pick up a single 2D material and then sequentially 'stamp' its atomically flat lower surface onto additional crystals. The van der Waals forces at this perfect interface cause adherence of these crystals, enabling us to construct flawless stacks of up to 8 layers."
After successfully demonstrating the technique using microscopic flakes mechanically exfoliated from crystals using the 'sticky tape' method, the team scaled up the ultraclean transfer process to handle materials grown from the gas phase at larger sizes, achieving clean transfer of mm-scale areas. The ability to work with these 'grown' 2D materials is crucial for their scalability and potential applications in next-generation electronic devices.
Recognising the significance of the breakthrough, The University of Ò°ÀÇÉçÇø has filed a pending patent application to safeguard both the method and apparatus involved. The research team is now eager to collaborate with industry partners to assess the effectiveness of this method for the wafer-scale transfer of 2D films from growth substrates. They invite expressions of interest from equipment manufacturers, semiconductor foundries and electronic device manufacturers with 2D materials in their product roadmap. For enquiries, please contact contact@uominnovationfactory.com
The National Graphene Institute (NGI) is a world-leading graphene and 2D material centre, focussed on fundamental research. Based at The University of Ò°ÀÇÉçÇø, where graphene was first isolated in 2004 by Professors Sir Andre Geim and Sir Kostya Novoselov, it is home to leaders in their field – a community of research specialists delivering transformative discovery. This expertise is matched by £13m leading-edge facilities, such as the largest class 5 and 6 cleanrooms in global academia, which gives the NGI the capabilities to advance underpinning industrial applications in seven key areas: composites, functional membranes, energy, membranes for green hydrogen, ultra-high vacuum 2D materials, nanomedicine, and characterisation.